Technical Overview
Pump Head / Cold End
KRYTEM piston pumps were developed specifically to overcome the physical challenges associated with delivering low-boiling-point liquefied gases. Localized evaporation caused by differences in pressure and temperature leads to the formation of gas bubbles. As a result, gas can enter the displacement chamber along with the liquid, even if conditions on the suction side are favourable, thus preventing the cylinder from filling completely and effectively reducing the discharge rate. The collapse of the bubbles during the push stroke makes a lot of noise (cavitation), and accelerates the wear and tear of the valves, piston and seals.
With this in mind, KRYTEM pump heads are designed to block, to the highest degree possible, any ingress of heat and loss of pressure when the medium flows into the cylinder. Heated or evaporated medium is removed from the pump head preventing it from entering the displacement chamber.
A vacuum-insulation effectively shields the cold parts of the pump from the ambient air temperature. To remove frictional heat generated inside the pump, the the cylinder bush is enveloped in discharge medium as well. The movement of the piston forces the medium in the direction of discharge through the pressure valve and also circulates the surrounding fluid. Warmed medium can freely ascend in the gas return feed and return to the tank by means of natural convection, subject to the existence of a suitable tank connection.
The oscillating piston rod is sealed by a spring-energised packing of multiple lip seal elements. The sealant effect at the piston rod surface is supported by the fluid (tank) pressure. A heating system and a bellow-type jacket at the gear end of the packing contribute to keeping the seal packing dry and clean of dust over a long service life and permit to maintain the pump in cold stand-by condition during longer operational breaks. In continuously operated facilities the service condition of the seal packing can be monitored steadily.
Drive Units
KRYTEM pump drives are extremely resilient and permit high discharge rates at comparatively low stroking speeds (typically 150 to 240 min-1, max. 300 min-1), even in the presence of high ultimate pressures. This makes the occurrence of cavitation less likely resulting in a more stable behaviour of the pump during operation, even under less-than-perfect operating conditions. Since the pump is exposed only to small amounts of dynamic stress, there is less wear on the pump head, eccentric drive and transmission drive in comparison to pumps featuring drives with higher stroking speeds. As a consequence, maintenance and operating costs are lower, too.
KRYTEM pumps for high-pressure applications and/or high discharge rates are driven by 45mm stroke Type F or 60mm stroke Type DF eccentric drives via a V-belt or toothed-belt transmission and an electric motor. For smaller discharge volumes and/or lower operating pressures, eccentric drive units with integrated reduction gears and max. 30mm adjustable stroke are available.
For high flow capacities duplex (two cylinder) or heavy duty triplex (three cylinder) solutions are available.
When operating under high pressure, strong forces are transmitted by the eccentric drive unit. An effective lubrication is essential for a reasonably long product lifetime. The separation of the pump head from the oil-tight drive housing by a long distance piece and the protective bellow at the seal packing end permit a safe use of standard hydrocarbon-based lubricants when delivering oxygen or other oxidising media. Alternatively, an oxygen-compatible lubricant is available for the F- / DF-series drive units.
Pump Control
KRYTEM pumps can be integrated into the higher-level automatic control loops of larger plants (e.g. for the automated supply of N2 or O2 to processes) but in most cases they are subject to a semi-automatic process monitoring via a KRYTEM control panel. Beside standard relays-based control designs KRYTEM offers PLC controls with standard modules of tailor-made client solutions.
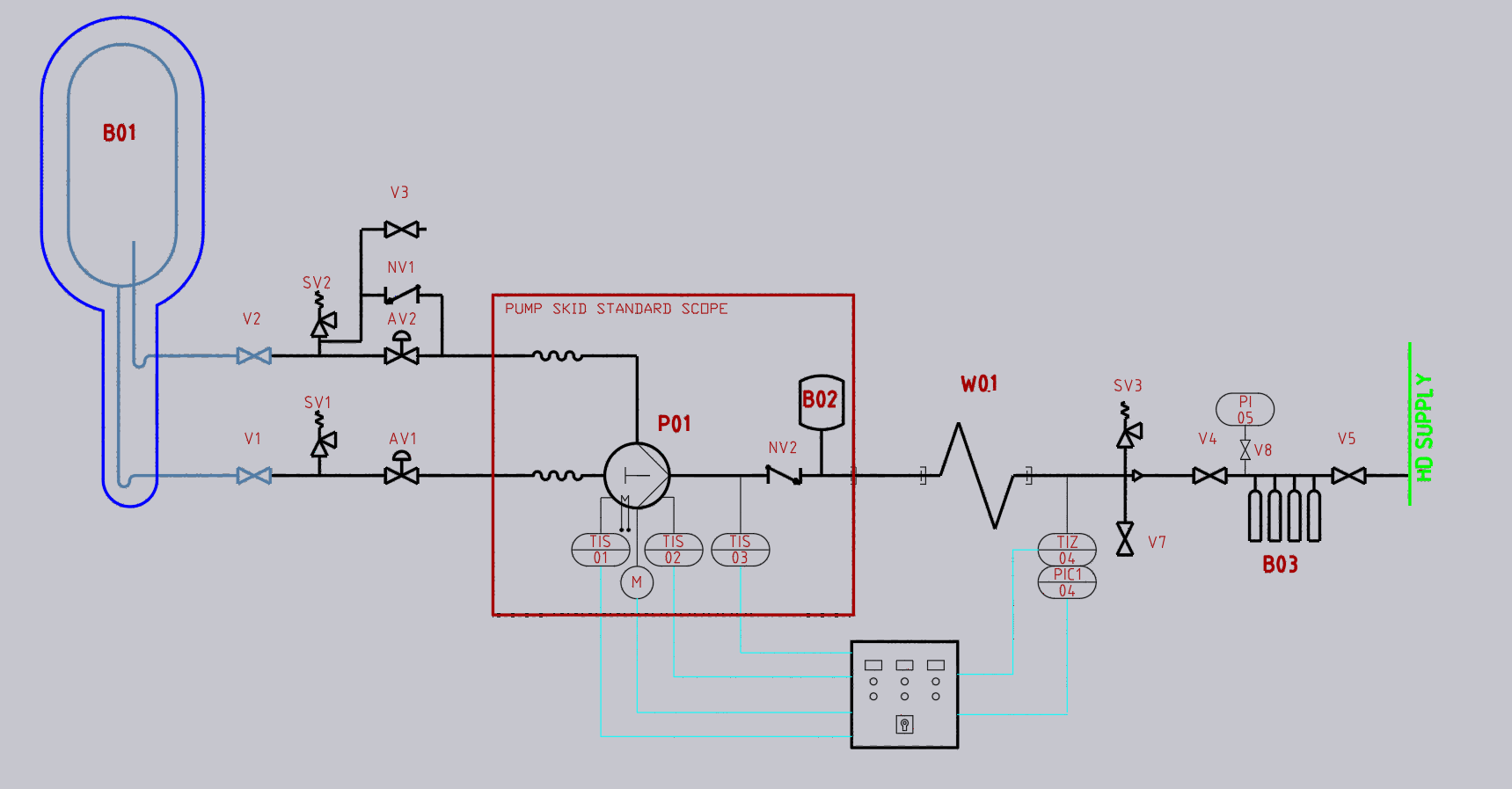
Standard pump installation: Control devices
Standard control set for pumps with single speed motors
- automatic start function and cool-down interlock
- flow monitor / dry-running protection
- piston seal temperature control and condition monitoring
- external start/stop and emergency stop interface
- hours counter
Options
- implementation of actuated inlet valves for automatic cool down and stand-by control
- manual or automatic speed adjustment for dual speed or variable speed pumps (VFD)
- gas temperature monitoring for cold-embrittlement protection
- automatic pressure control
- automatic pump stop at target pressure, manual restart – e.g. manual gas cylinder filling
- automatic start and stop – e.g. unattended / automatic buffer filling for process supplies
- pump speed reduction when approaching target pressure
available for dual speed or variable speed pumps - steady pressure control with variable speed pumps – e.g. for high pressure process supplies
- vaporiser or trim heater control